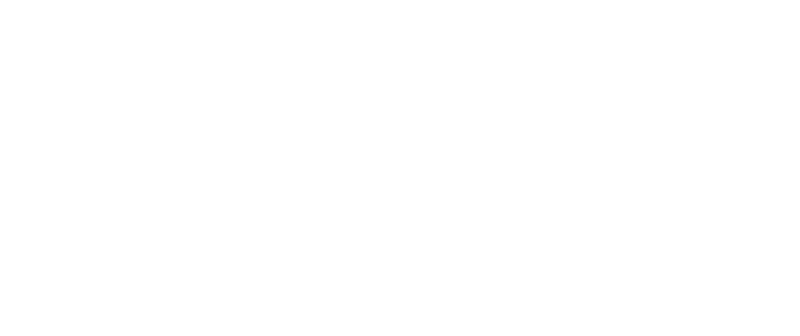
E-Mobility – secure connections HEV, BEV und FCEV
About ten years ago, we cooperated with an OEM to design the first connection technology for geared motors. This led to the development of the e-traction/power train division for geared motors in the e-mobility sector, which extends to fully automated production. Our applications in the HEV, BEV and FCEV sectors also include:
- power distribution via busbar wiring systems and associated components,
- connections of plug-in systems to high-voltage cables,
- connections from busbars to cables and braids for module connectors of the individual high-voltage storage units (butt welding or overlap welding),
- connections in the high-voltage electrical system from the battery to the inverter or from the inverter to the electric motor up to the phase connection in the CCS,
- connections in ECUs,
- electrical components,
- traction distributors,
- pyro fuses,
- connection technology in geared motors (phases and star points) as well as connections to current rings.
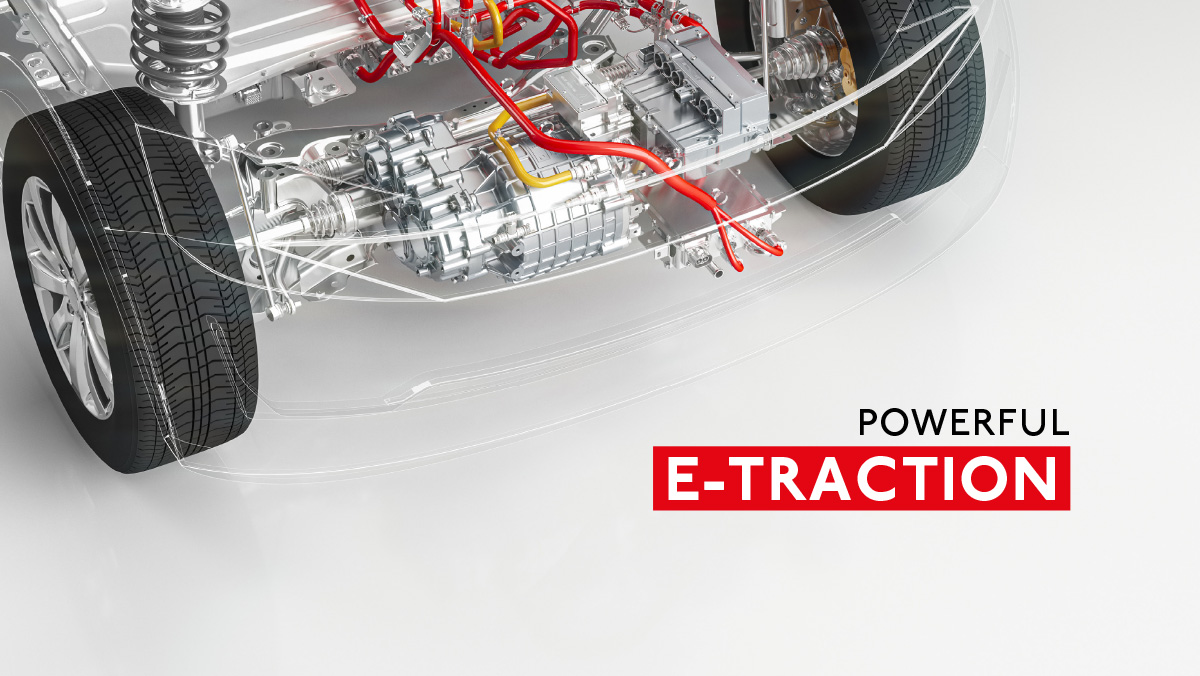
Safety in high-voltage on-board systems
In general, cable harnesses in EVs involve welding of high-voltage connector systems to high-voltage (HV) cables with cross-sections of 25 to 120 mm² for cable connector systems or busbars. Traction distribution systems for four-wheel-driven e-mobility with cross-sections of up to 300 mm² are also part of our portfolio.
Absolute reproducibility in the connection is of the utmost importance here, as there is a risk of fire in the event of a field failure. For this case, we have developed systems for welding under braze that enable fully automatic production including monitoring.
Individual product-related traceability is guaranteed by our specially designed STRUNK MES software. This makes the required data available in an SQL database by networking the systems in individual production steps within the automated production. Alternatively, the data records can be uploaded to your MES software as required.
In the field of HEV, BEV and FCEV e-drives, connections can be created for wound stators or hairpin stators. The former are joined using hot crimp technology while hairpin stators are connected by resistance brazing. Both result in reliable, non-ageing material-to-material connections.
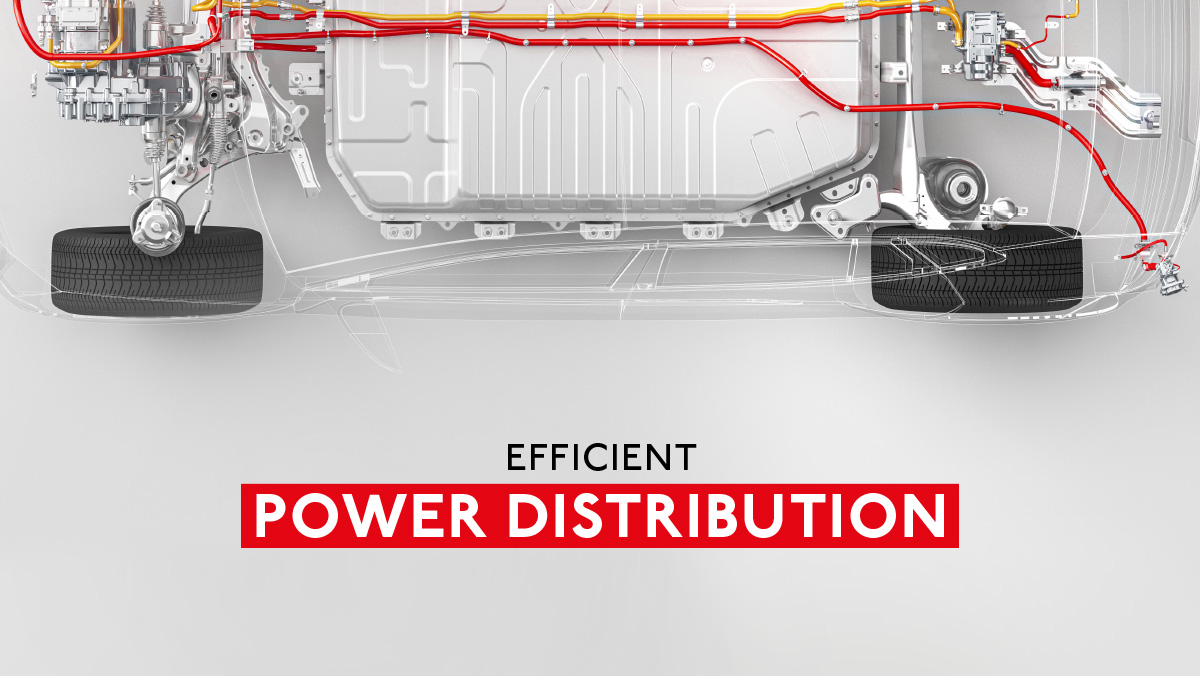
High-voltage cable set and module connectors
Cable and non-ferrous metal connections in EVs must be designed to withstand high current loads. Furthermore, the contact resistances at the connections must be kept close to zero. If these requirements are not guaranteed, this results in heating (hot spots), which lead to field failure due to further increasing resistance. We therefore aim to achieve transmission with as little loss as possible.
Additionally, the mechanical holding forces are extremely important to avoid high-impedance effects or loosening of the connection even under mechanical and environmental stress. In these cases, our technologies offer you options for achieving secure and demonstrably long-term stable connections even under high loads.
In the field of high-voltage technology, we develop and manufacture solutions for the following areas of application:
- e-traction: everything related to the power train, e. g. welding of phase connections and star points,
- connections to stators using winding and hairpin technology,
- connection technology for rotors,
- connection technology in assembly (phase connection to terminal boards),
- power distribution/busbars/lead frames: HV electrical systems, busbar electrical systems in vehicles,
- HV storage systems: development of new technologies for battery cell connectors (HV cable set),
- connection technology from HV cables to HV connectors,
- AC/DC charging systems and
- pyro fuses.
We can also connect components for HV wiring using the methods of overlapping or butt welding under braze.
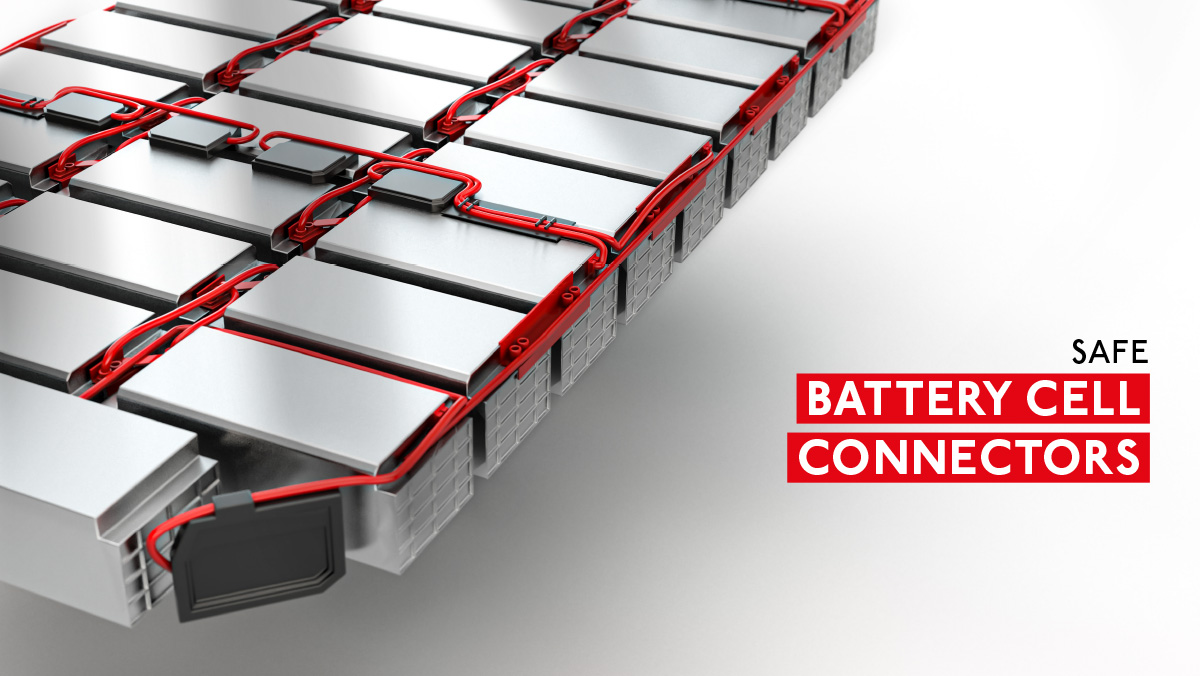